10 Tips to Save Your Combustion Equipment in Electrical Outages
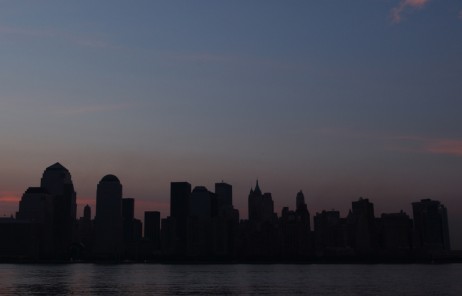
It is better to be prepared for an emergency and never have to use it, than to have an emergency happen and not be prepared. For this reason, preparing your combustion equipment for electrical outages is very important. In this article by Jason Safarz from CEC Combustion Safety he reviews 10 tips that will help save your combustion equipment during an outage.
From earthquakes in California, to tornados in Kansas, to hurricanes in Florida, natural disasters occur everywhere. Natural disasters damage power plants, destroy gas lines, disrupt power grids and create blackouts, causing combustion equipment to go offline. Understanding how to prepare for electrical issues is imperative to minimize loss for any combustion-related catastrophes. Electrical power issues come in many forms but can have the same combustion system impact.
To help head off problems before they occur, here are 10 combustion equipment tips related to electrical power issues. Whether or not you have been affected by a natural disaster, pay attention and reevaluate your electrical systems to make sure they are not taken offline in an unsafe manner or damaged if a loss of power happens in your area.
1. Prepare for BMS Failure Issues
A burner management system (BMS) can be destroyed by a power outage, and without a BMS, your business could be out of service for a few hours — if you have a spare that is still supported by the manufacturer — or even a few days if you do not have a spare on hand. If your system is an older electromechanical style, you are vulnerable to being out of service for many days. Obsolete BMSs must be upgraded when changed out. This often requires a complete rewire of your control panel or finding and ordering a new BMS in a crisis mode.
The best practice is to make sure that you have a spare BMS at your facility, or that you have ready access to one. When you consider the potential for loss, a few thousand dollars for an additional BMS is a worthy investment.
2. Avoid Loss of Cooling for Fans, Doors and Bearings
Sometimes, cooling water is designed into oven doors and cooling bearings on fans. Forced-draft and induced-draft fans on boilers also can have water-cooled bearings. A problem results when this water flow is not alarmed, or the loss of this water flow is not alarmed. If the water were to be interrupted due to a city, municipal or booster pump problem, it can instigate major trouble. Some plants recirculate water and rely on city water as a backup. In some disaster situations though, even the city’s backup water is not available.
To avoid this obstacle, backup generators should have recirculated water pumps, and cooling water must have a backup system or some type of flow or temperature alarm. In addition, these alarms and backups are required to be tested regularly for proper operation.
3. Know that System Failure Modes Can Mean Trouble
It is important to know at what position each part of your combustion system is configured to fail in the case of a power interruption. For example, in what position will damper linkages or boiler feedwater valves end up: fully open, at their last position or fully closed? The wrong position can be disastrous. Control systems must be configured to make for a safe startup after unexpected equipment shutdown.
If the BMS does not provide a lockout circuit, some equipment may restart automatically when the power is restored.
Key interlocks must be reset manually. Manual reset requires a person to physically press the reset button to restore operation. Without the manual reset feature, equipment can instantly restart without warning, which can be extremely dangerous and damage critical equipment components after momentary — let alone extended — outages.
4. Startups Can Be Challenging
Starting up is always a cause for concern. If you shut down instantaneously at high fire with no planning, you could have a firebox with enough fuel in it to be flammable. It would only take a hot ignition source for an explosion to occur. Remember that in some cases, adding purge air to a firebox that already contains fuel and a hot ignition source also can create the right conditions for an explosion.
Recall your combustion basics: it is all about fuel, air and heat as an ignition source. Attempt to restart only after the firebox has had a chance to cool off.
5. Improper Shutdowns Can Cause Trouble
Shutting down in a hurry means large-diameter oven fans do not get a chance to cool down as the manufacturer intended. Many oven shutdown procedures call for ventilation and recirculation fans to continue to operate after flame failures and during orderly shutdowns to protect them from overheating and warping.
If you are forced to shut down with no time for cooling, be careful to listen for noises and vibrations during startup. These indicators mean that you have damaged fans, bearings or shafts. It also signifies that the equipment is no longer safe to operate in that condition.
6. Do Safety Switches and Interlocks Work Correctly?
When equipment does not operate correctly, processors rely on safety controls such as high gas pressure switches, low gas pressure switches, airflow switches and flame detectors to keep the plant and personnel safe. When facilities experience power outages, systems are definitely not operating correctly yet processors still rely on this equipment to work.
Consider the case of airflow not being correct due to a loss of fan power or voltage during a brownout or a full blackout. In such situations, it is imperative to have properly functioning airflow switches to ensure that fuel valves do not remain open. NFPA requires that all safety interlocks be tested at least annually by qualified personnel and work at the right setpoints.
7. Be Aware of Refractory Damage Vulnerability
When bringing systems back up, be certain to check for signs of failed refractory. Some equipment is prone to refractory failures after an outage because the refractory brick is thermally cycled. This is something you must be aware of during any startup. Refractory failures are indicated by glowing hot spots on equipment, or burned paint or changed surface colors on the outside of equipment walls.
8. Avoid PLC Configuration Issues
If you have programmable logic controllers (PLCs), you may be surprised by how they are configured during a post-power-loss startup. Your system most likely will recover to whatever was recently stored in the EEPROM, or non-volatile memory. Volatile memory relies on power to the equipment and would be lost during a shutdown. You must be aware of this and ensure that the post-power-loss startup configuration of your system is safe.
If you have PLC controls, now is a good time to confirm that your backup memory storage batteries are in proper working order. Functioning backup memory could be the difference between safety and a disaster.
9. Remember that Special Atmospheres Can Be Trouble for Heat-Treat Ovens
Remember that heat-treat operations utilizing special combustible atmospheres are extremely vulnerable to power loss issues. In these cases, you must get the atmosphere out and safely burned off, or a catastrophe can result. This means having inert gases like nitrogen available to push the atmosphere out in an orderly manner or having a manual burnout procedure in place. Make sure all control systems are built and configured to get purging materials to the appropriate area even under power-outage conditions.
10. Handle Pressure Surges and Steam Safety-Relief Valves
The sudden loss of power in a major manufacturing facility could result in control valves unexpectedly slamming shut. This means that a great deal of steam already in the system is flowing toward the valve, but abruptly, there is no place for it to go. Steam is something that does not instantaneously stop being generated.
When this happens, safety-relief valves should pop open. If they do not open, equipment can blow apart and people can be seriously injured or worse. Now more than ever, processors must embark on a safety-relief valve-testing program. Per NFPA, safety-relief valves must be lift tested or verified to operate at least once a year. If you have never tested before, be sure to seek out guidance first. You can damage valves or get hurt if the testing is conducted incorrectly.
Learn more here.
Looking for a new heating system that is customized to fit your needs? Call Heatrex today at 314-644-4300 or visit us at www.heatrex.com.