Process Air Heaters
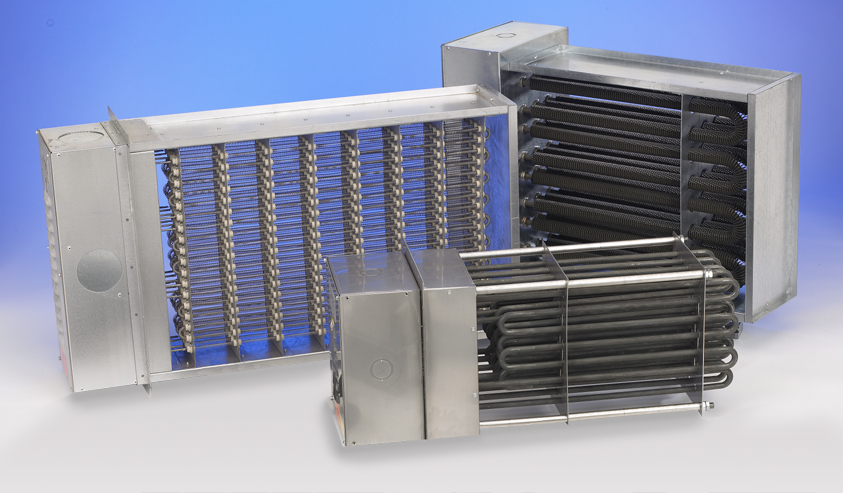
Does your industry have a need for a forced air heating system? Heatrex will design a custom process air heater for your need that is efficient and economical! At Heatrex, we have a reputation for designing and manufacturing high quality process air heaters that will meet most applications!
Construction
Heatrex process air heaters are designed and built with the following construction features to assure the highest quality and long service life.
OPEN COIL HEATERS:
- Minimum bracket spacing that reduces coil sag.
- Galvanized steel framing up to 250°F outlet air; Aluminized steel framing up to 600°F outlet air; 304 stainless steel for temperatures up to 1200ºF.
- Heavy gauge steel flange with pre-drilled mounting holes for 400°F outlet air and higher.
- Stainless steel terminal hardware and 10-32 threaded studs for reliable connections.
- For NEMA 1 applications a Terminal box with a louvered cover ensures that the connections and wiring stay at safe operating temperatures.
- Pressure connectors that are welded or bolted onto bus bars for field wiring of 8 gauge and heavier.
- Removable bus bars that are secured with stainless steel nuts and shake-proof washers.
- Rib-strengthened brackets with formed gussets at corners for rigidity.
- 80/20 Nichrome coils for minimum sag and maximum life.
- Multiple concentric knockouts on all sides of the terminal box for convenient conduit entry.
- 1″ of insulation in the terminal box is standard for outlet temperatures up to 750°F. 4″ insulation below the mounting flange is standard for 1200°F construction. It may be optional for other constructions.
FINNED TUBULAR HEATERS:
- Aluminized steel support brackets that have flared openings allow elements to expand and contract smoothly.
- Elements are 0.475″ in diameter, 304 stainless steel with corrugated fins, 1-⅛” O.D. are the same material.
- Heavy steel or stainless steel flanges with pre-drilled mounting holes are furnished for 400°F outlet air and higher.
- Multiple concentric knockouts on all sides of the terminal box for convenient conduit entry.
- Stainless steel terminal hardware and 10-32 threaded studs to assure reliable connections.
- Removable bus bars are secured with stainless steel nuts and shake-proof washers.
- Terminal box may be side or top mounted.
- The louvered terminal box cover for NEMA 1 designs keep the temperatures safe for the connections and wiring.
- Individually replaceable elements mounted to the terminal flange with push nuts.
- Optional 4″ insulation below mounting flange that cuts energy losses through oven walls, keeps electrical connections cool. 1″ of insulation in terminal box is standard for 400°F and 600°F outlet air.
- ½” diameter steel rod that tie the assembly together in a rigid, but expandable mode.
- Open framework that allows universal mounting that can be used with either horizontal or vertical airflow.
- Pressure connectors that are welded or bolted to the bus bars that are furnished for field wiring of 8 gauge and heavier.
TUBULAR HEATERS:
- Heavy steel or stainless steel flange with pre-drilled mounting holes.
- Multiple concentric knockouts on all sides.
- Louvered terminal box cover.
- Pressure connectors welded or bolted to bus bars.
- Bus bars are removable and secured with stainless steel nuts and shake-proof washers.
- Elements are individually mounted with push nuts to allow replacement of the individual elements.
- Stainless steel terminal hardware and 10-32 threaded studs.
- 304 stainless steel support brackets with contoured openings to allow elements to expand and contract.
- ½” diameter steel rods.
- Recompressed bends that prevents hairline cracks in insulation that extends the element’s life.
- Elements are 0.475″ diameter Incoloy 800 sheath.
- Unique bending configuration that reduces the number of element terminals by more than half, lowering terminal box temperatures.
- Terminal box may be side or top mounted.
- 1″ insulation for up 750°F. 4″ insulation below mounting flange standard for 1200°F. Optional for other constructions.
250°F CONSTRUCTION
- •Low temperature heaters, suitable for 250ºF maximum outlet air, are available in both open coil and finned tubular constructions. They are identical to the heaters described above except for the following features. The steel flange is omitted and the heater is attached to the oven or duct wall with sheet metal screws through the base of the terminal box.
- Individually replaceable finned tubular elements are flanged mounted.
- Terminal box has a 1″ insulation.
- A galvanized steel channel frame is provided on three sides, with the element support brackets welded to the frame.
Applications
These heaters can be installed in plenums, ducts, or pipes to heat forced air in industrial equipment and systems. There is vast variety of heater designs and sizes available to provide outlet air temperatures up to 1200°F.
The air that is used could be either fresh or recirculated. Fresh air may be used when ventilation of the process is necessary. Recirculated air is used to reduce power consumption and the heater size.
Process air heaters can be installed in ovens, furnaces, autoclaves, dryers, conveyor systems, pressure vessels, and other equipment that can supply these types of applications:
- Aircraft Manufacturing
- Air Curtains
- Air Drying
- Annealing
- Booster Heating
- Baking
- Batch Heating
- Chemical Processing
- Cooking
- Core Drying
- Cryogenic Exhaust gas heating
- Curing
- Dehumidification
- Dehydrating
- Drying
- Exhaust Gas Heating
- Film Drying
- Finishing Systems
- Food Processing
- Fruit Ripening
- Heat Recovery Supplement
- Heat Treating
- Hopper Heating
- Ink Drying
- Laboratory Testing
- Make-up Air Heating
- Metal Finishing
- Motor Winding Burnoff
- Paint Baking/Drying
- Pharmaceutical Manufacturing
- Plastic Curing
- Preheating
- Reheating
- Roasting (nut, coffee, corn, etc.)
- Semiconductor Manufacturing
- Sterilizing
- Standby Heating
- Textile Drying
- Varnish Drying
- Wire Manufacturing
Correct Watt Density
A critical factor in heater selection is watt density. A heater’s life can be diminished if the watt density is too high for the application. If the watt density is too low, the heater cost will be high.
Proper watt density has three variables to function:
- Heater construction
- Maximum outlet air temperature
- Air velocity
Circuit Sizing
All standard heaters have circuits that draw a maximum of 48 amps and this enables the use of 50 amp contactors and 60 amp fuses that are generally less expensive than higher rated devices.
Larger circuits are desirable for certain application that may use large SCR controls or to reduce the number of incoming power conductors. In these cases, larger circuits up to approximately 300 amps can be provided.
Calculating KW Requirements
To determine the kilowatt rating (kW) the volume of air in standard cubic feet per minute (SCFM) and the required temperature rise in °F (T) need to be known. Here is the formula:
Heatrex will provide quality process heaters that will provide heat for most types of heating applications your industry may use. If you would like to speak with an Heatrex representative please visit our website: www.heatrex.com.